Collision with terrain
Privately registered
De Havilland DHC-2 (Beaver), C-GSBA
Campbell River Airport, British Columbia, 10 NM SSE
The Transportation Safety Board of Canada (TSB) investigated this occurrence for the purpose of advancing transportation safety. It is not the function of the Board to assign fault or determine civil or criminal liability. This report is not created for use in the context of legal, disciplinary or other proceedings. See Ownership and use of content. Masculine pronouns and position titles may be used to signify all genders to comply with the Canadian Transportation Accident Investigation and Safety Board Act (S.C. 1989, c. 3).
History of the flight
On 20 September 2023, the De Havilland DHC-2 (Beaver) aircraft (registration C-GSBA, serial number 690), which was privately registered to Sealand Aviation Ltd.,Sealand Aviation Ltd. “overhauls, rebuilds, salvages and repairs aircraft. [It] also manufactures aircraft modification kits and components. The company is Transport Canada approved for structures, maintenance, welding and manufacturing.” (Source: Sealand Aviation Ltd., at sealandaviation.com [last accessed on 18 July 2024].) was conducting a visual flight rules familiarization flight from and to the Campbell River Airport (CYBL), British Columbia (BC), with 2 pilots on board.
The aircraft was equipped with a RED A03-005 reciprocating diesel engine, manufactured by Raikhlin Aircraft Engine Developments GmbH (RED) of Germany. This combination of airframe and engine was a prototype design being developed by Sealand Aviation Ltd. The occurrence flight was authorized under a specific purpose flight permit (see section Flight authority).
The pilot-in-command (PIC) was familiar with the aircraft. The co-pilot was an accredited test pilot and was undergoing aircraft familiarization for the purpose of participating in the future test flight program for the prototype aircraft. This type of training flight was among the flight operations allowed by the specific purpose flight permit.
During the flight, a power-off stall exercise was conducted at an altitude of approximately 4000 feet above sea level (3340 feet above ground level). At approximately 1031,All times are Pacific Daylight Time (Coordinated Universal Time minus 7 hours). when power was commanded from the engine during recovery from the stall, the aircraft did not produce sufficient thrust to maintain altitude, and a forced landing was carried out (Figure 1). The aircraft came to rest in a heavily wooded area, approximately 10 nautical miles (NM) south-southeast of CYBL. The pilots received minor injuries, but both were able to egress the aircraft. They were taken to hospital by a search and rescue helicopter.
The aircraft was substantially damaged. There was no post-impact fire. The emergency locator transmitter (ELT) activated.
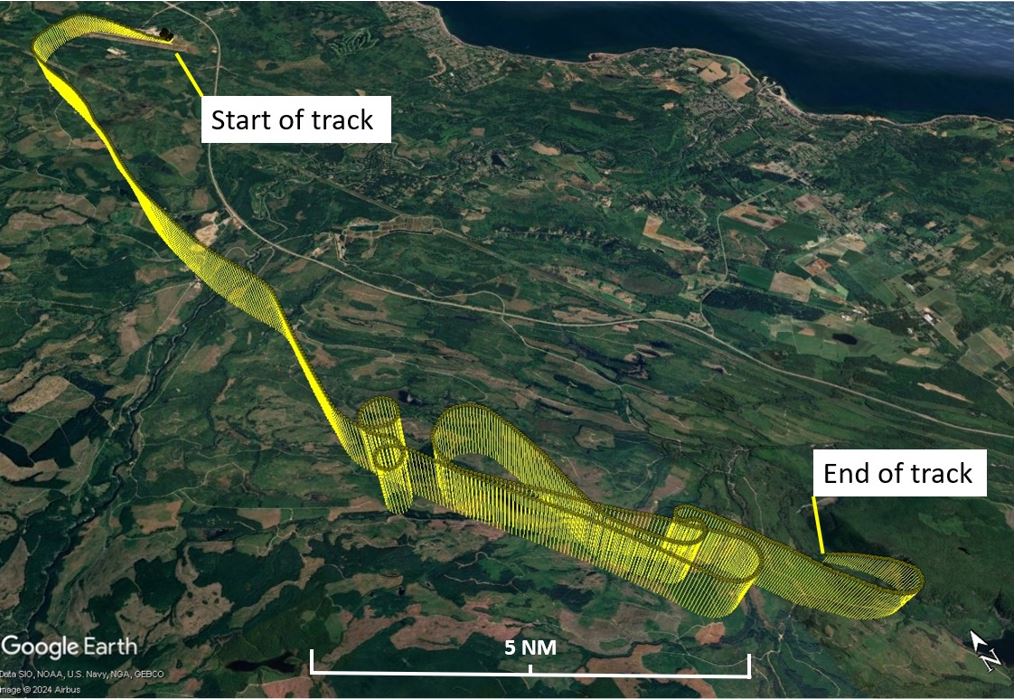
Pilot information
The PIC, who was seated in the right seat, held the appropriate licence and rating for the flight in accordance with existing regulations; he held a commercial pilot licence with ratings for land and seaplanes. Before the occurrence, the pilot had acquired more than 8500 total flight time hours. Approximately 3600 of those hours were on the conventionally powered version of the DHC-2 aircraft, and approximately 20 hours were on the occurrence aircraft.
The pilot receiving familiarization training, who was seated in the left seat, held an airline transport pilot licence with ratings for land and seaplanes. Before the occurrence, he had acquired approximately 15 000 total flight time hours. He did not hold a valid aviation medical certificate at the time of the occurrence; however, given that he was not acting as the PIC for the flight and that the aircraft was approved for single-pilot operations, he was not required to hold one.
According to information gathered during the investigation, there was no indication that the performance of either pilot was affected by medical or physiological factors.
Aircraft information
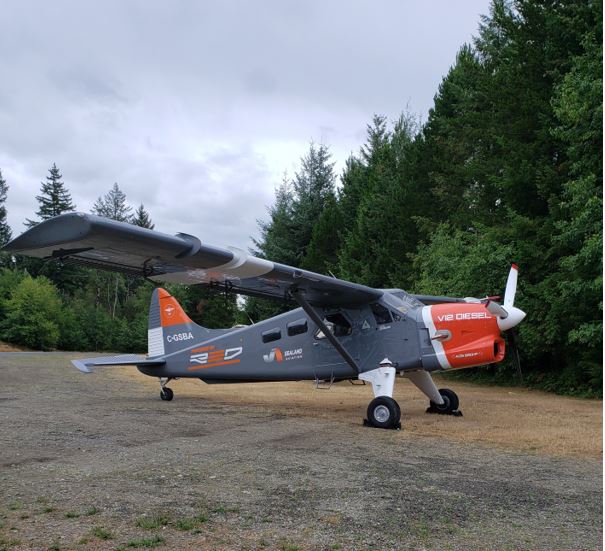
The occurrence aircraft (Figure 2) was manufactured by De Havilland Aircraft of Canada Ltd. in 1954. It was operated by the United States (U.S.) Army before being sold to a civilian operator in the U.S. in the 1970s. In June 2020, the aircraft was registered privately in Canada to Sealand Aviation Ltd. and was subsequently partially disassembled and rebuilt. During this rebuild, the aircraft was equipped with a RED A03-005 engine.
Engine information
The RED A03-005 engine (Figure 3) is a 12-cylinder, twin turbocharged, high-compression-ignition engine with two 6-cylinder banks capable of independent operation. The engine is controlled by a full-authority digital engine control (FADEC) system, which is in turn controlled by an electronic engine control unit (EECU). A single cockpit lever is used to command both the engine power and the blade angle of the reversing MT-Propeller GmbH MTV-9-E-C-R(M) variable-pitch propeller driven by the engine. The propeller rotates counterclockwise (as viewed from the pilot’s seat) at a maximum of 2127 rpm. The engine is rated to a maximum of 550 hp and is approved for operation with kerosene-type fuels, including jet fuel.
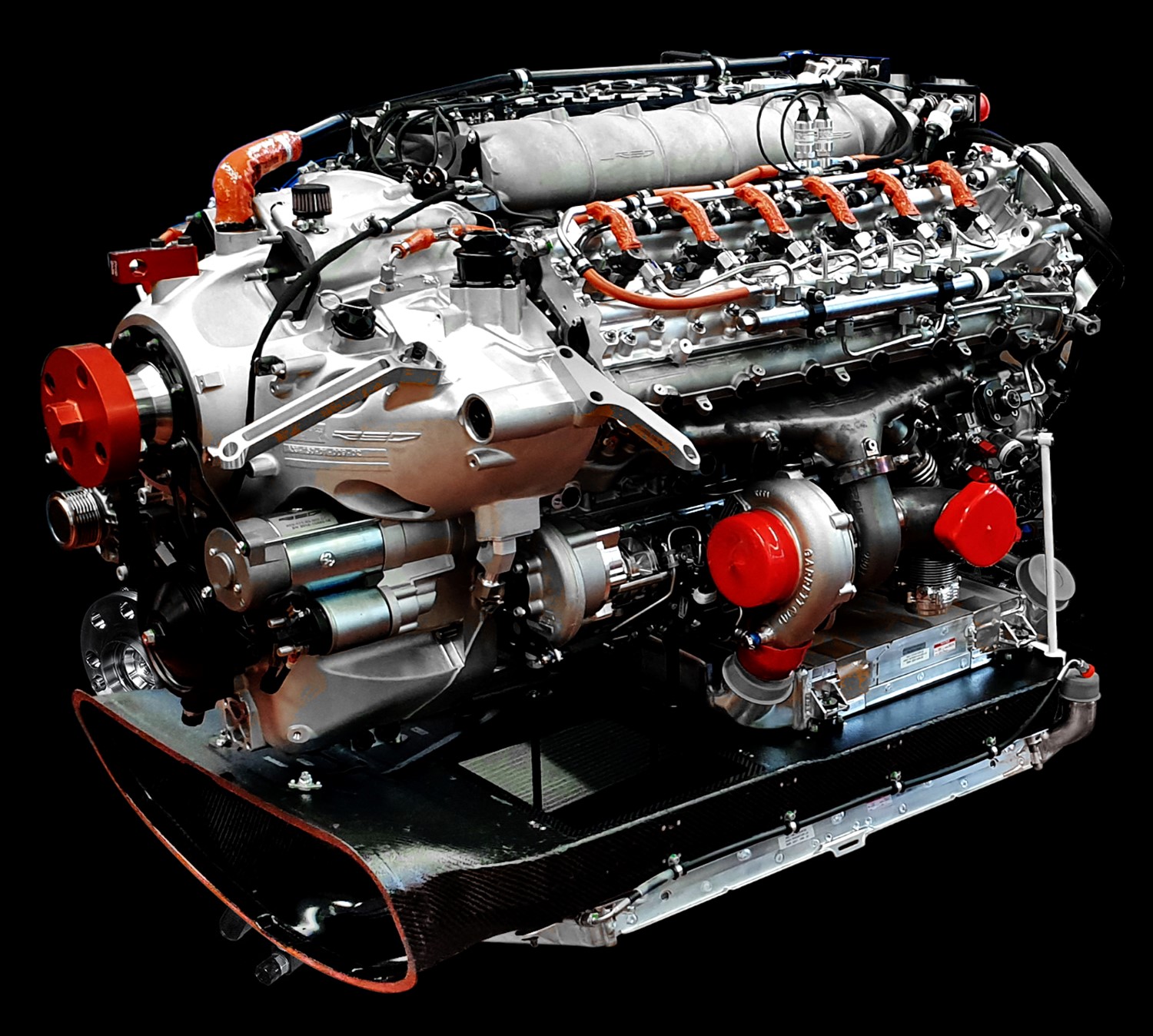
The RED A03-005 engine is type certificated in Europe by the European Union Aviation Safety Agency and in the U.S. by the Federal Aviation Administration At the time of the occurrence, a Canadian type certificate had not been issued for the engine. However, the engine was authorized to be used on the Canadian-registered occurrence aircraft subject to the conditions stipulated in 2 flight permits issued to the operator by Transport Canada (TC): an experimental flight permit and a specific purpose flight permit.
Flight authority
The experimental flight permit issued by TC authorized a flight test program for the purpose of developing a supplemental type certificate that could allow for a certified installation of the RED A03-005 engine on the DHC-2 airframe once the engine was certificated in Canada. The specific purpose flight permit allowed for demonstration and training flights on the aircraft. Either permit could be brought into force via an entry in the aircraft journey logbook; however, the aircraft could not be operated under both permits concurrently—only 1 flight authority could be in effect at a time.
Both permits required the aircraft to be configured and equipped in accordance with a technical drawing specified by the permits. Any modifications made to the aircraft that deviated from this configuration would require consultation with TC as well as the issuance of a revised flight authority.
The investigation determined that the aircraft was modified after the 2 flight permits had been issued and that it was being operated in this modified state. The investigation also determined that the modifications did not comply with the intended conditions and limitations specified by the permits, and they had not been communicated to TC for the issuance of a revised flight authority.
Furthermore, the investigation determined that the technical drawing referenced by the issued flight permits was incorrect. Rather than detailing the complete configuration of the aircraft, the referenced drawing was limited to details of the aircraft’s engine mount.
Aircraft maintenance and modifications
Some modifications made to the aircraft, including changing the propeller governor system, did not conform to the intended conditions of the flight authority. The investigation determined that the original reversing propeller governor (Governor No. 1) was removed from the engine due to difficulties encountered during aircraft operations. A non-reversing propeller governor (Governor No. 2) was installed, and the aircraft was operated under its experimental flight permit. Approximately 2 months later, a prototype reversing propeller governor (Governor No. 3) was installed, but it was removed before the aircraft was flown, and the non-reversing propeller governor (Governor No. 2) was reinstalled. This was the model installed on the aircraft at the time of the occurrence. None of these changes were documented in the aircraft’s maintenance or technical records.
The propeller governorMT-Propeller model P-983-43D. authorized for use under the aircraft’s flight authority (Governor No. 1) was designed to be used with a reversing propeller. The propeller governorMT-Propeller model P-883-50K. found installed at the time of the occurrence (Governor No. 2) was not designed for use with a reversing propeller. Both propeller governors are electronically controlled single-acting systems that use oil pressure to decrease propeller pitch; however, they differ with respect to their oil pressure output.
The propeller governor installed at the time of the occurrence (Governor No. 2) was determined to have an output oil pressure sufficient to drive the propeller blades into a reverse pitch angle at idle engine power under certain flight conditions. Once the propeller was established in reverse pitch, advancing the power lever would not reestablish a positive pitch with the installed propeller governor because the governor output oil pressure remained at the level required to produce reverse pitch. A reverse propeller pitch angle in flight creates a thrust vector opposite to the flight path. TSB laboratory analysis of the damage to the propeller system components determined that all 3 propeller blades were likely in the reverse blade angle range when the aircraft impacted terrain. This may explain why inadequate thrust was available following the power-off stall exercise.
Protection against unintentional reverse propeller pitch angles with the approved propeller and governor is normally provided by a mechanical system and an electronic system. The mechanical system is a physical lockout, which prevents a reverse pitch angle when the propeller rotation is above approximately 1400 rpm. The propeller rpm at the time of the occurrence is unknown. The electronic protection system was not compatible with the governor (Governor No. 2) installed at the time of the occurrence and had been disabled.
Weather information
The nearest aerodromes to the occurrence location that issue aerodrome routine meteorological reportsAerodrome routine meteorological reports are issued every hour and describe the current weather within a 3 km radius of the observation site. are CYBL, approximately 10 NM to the north-northwest, and Comox Aerodrome (CYQQ), BC, 13 NM to the east-southeast. The recorded weather was conducive to visual flight rules flight, and weather was not considered to be a factor in this occurrence.
Impact and wreckage information
The aircraft struck the ground in a heavily wooded area with uneven terrain (Figure 4). The wreckage showed signs of a low-energy, low-angle impact, consistent with a forced landing. The wings and landing gear were separated from the aircraft, with damage along the leading edges of the wings. All propeller blades received damage consistent with propeller rotation on impact. The fuel tanks in the aircraft’s belly were damaged, releasing an unknown quantity of fuel. The occupiable space within the fuselage was not compromised. There was no post-impact fire.
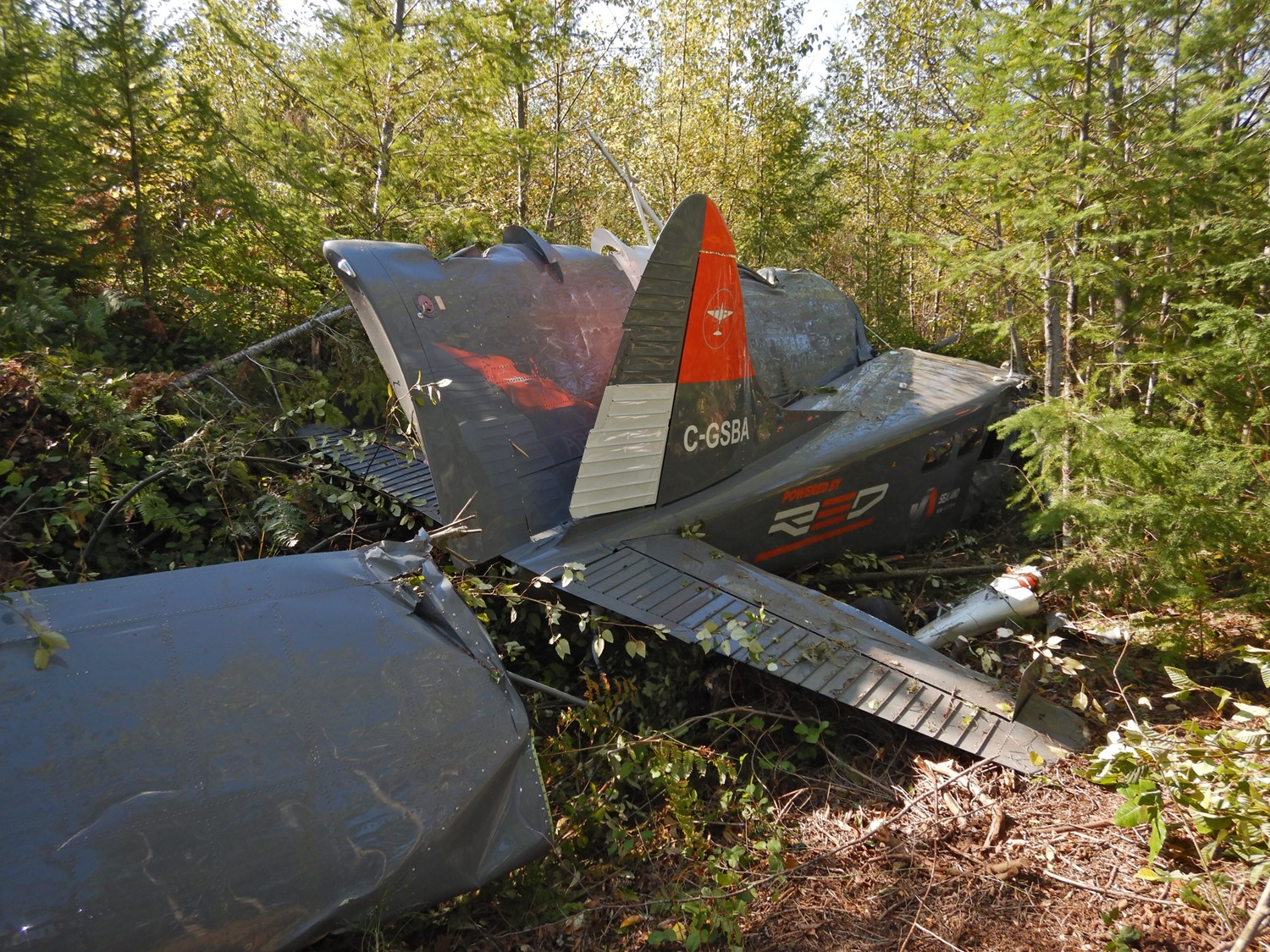
Survival aspects
The aircraft’s seats and restraints functioned as intended. The aircraft was equipped with 3-point restraints for both pilots.
Several aircraft exits were unusable due to fuselage compression or obstruction by aircraft debris and terrain features (Figure 5); however, the pilots were able to egress the aircraft unassisted via the left cockpit door.
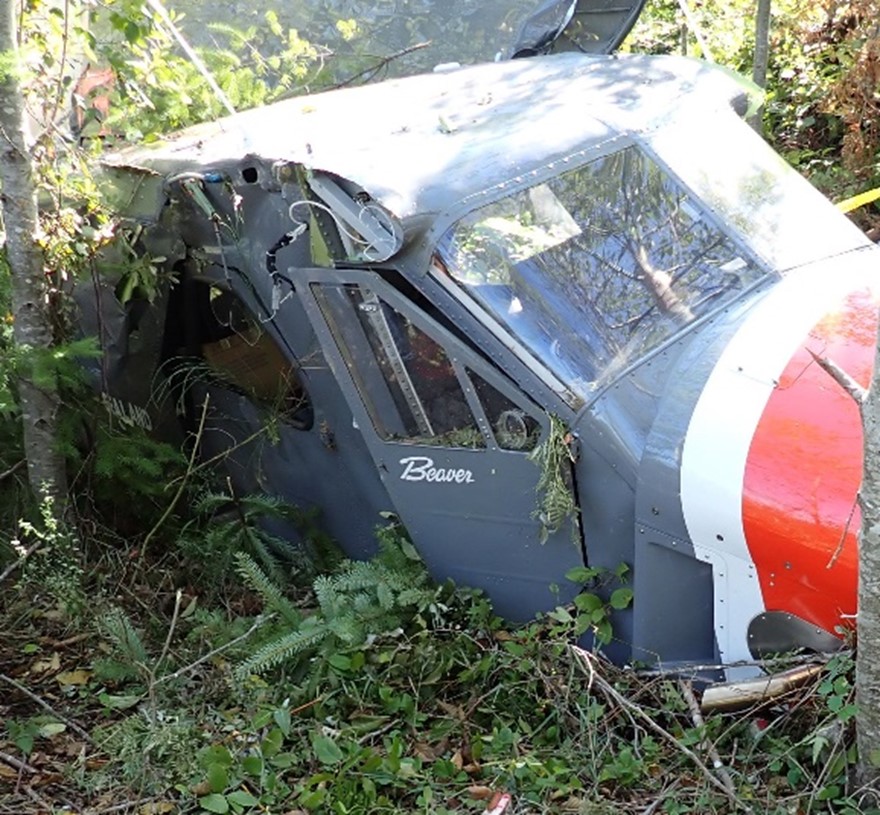
The aircraft was equipped with an automatic fixed 406 MHz ELT. Following the occurrence, the aircraft’s ELT activated automatically and broadcast a signal, which was received by the Cospas-Sarsat satellite system and assisted the Joint Rescue Coordination Centre in Victoria, BC, in directing search and rescue personnel to the location of the aircraft.
TSB laboratory reports
The TSB completed the following laboratory reports in support of this investigation:
- LP132/2023 – NVM Data Recovery - Various
- LP023/2024 – Propeller Hub Analysis
The U.S. National Transportation Safety Board supervised testing of the aircraft’s propeller and propeller governor system at the manufacturer’s facility in DeLand, Florida, U.S.
Safety message
Aircraft owners and operators are reminded that all maintenance must be properly recorded for aircraft documentation to serve as a reliable method of determining airworthiness and aircraft status. For the safeguards that result from the conditions and limitations listed in a regulatory flight permit to be effective, it is critical that aircraft be operated in accordance with the permit, and that any modification to an aircraft be approved before flight.
This report concludes the Transportation Safety Board of Canada’s investigation into this occurrence. The Board authorized the release of this report on 24 July 2024. It was officially released on 06 August 2024.